An Interesting Mastering Job
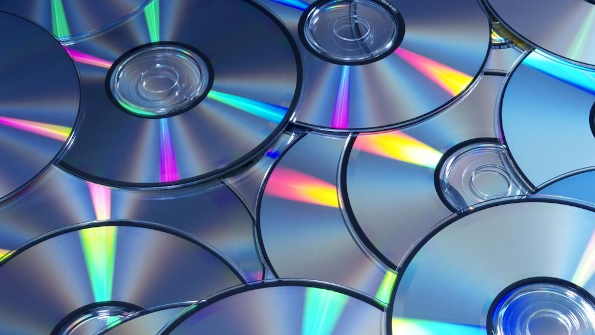
04/08/2021
I just completed the steps involved in mastering and fabricating a CD and I thought that perhaps watching me go through the process could help you understand it better. And yes, a CD. Believe it or not, people still use that medium and virtually all albums are still released in the format. This project was a dual release with both CD and streaming available to the audience. Let me start out by letting you know that this was a spoken-word CD, narration over music. The client chose to do this project right: they worked with a film and video soundtrack scoring composer to provide a through-score for the project. I should ‘fess up that I started on this job as the recording and mixing engineer and was then asked to master as well. Yes, yes, you should use separate mastering and mixing engineers, but I have been recording and mixing for forty years and mastering for about twenty of those years and work in an excellent control room, so filling both roles on this project isn’t so much of a reach.
So, this means I was THE engineer, soup to nuts, on this job. To give you an idea of the scope of the project, I recorded the voiceover talent at the beginning. I liaised with the scoring composer in Sweden and had him send me multitrack stems so I could properly balance the score and the voice. Mixing the voice and music might seem like a snap, but we treated this like a movie or music mixing project with the goal of making the voice sit on top of the music like it was the vocal in a song. What complicates this process is that when a typical scoring mixer provides a stereo mix, he rarely can separate himself from the intentions of his music to look at the whole product and protect the voice from too much activity in the score. With a stereo music mix, activity in one instrument section can challenge the voice, forcing the whole score to be dipped. That is where the stems come in. I spec’d the stems in such a way as to separate the instruments into sections and then to further separate the sections into one stereo pair with legato chords or drones and another with the activity, pizzicato strings, staccato stabs, melody lines, etc. The stems are mixed by the composer so that if all of them are pulled up to “0” on the faders we have unity gain, and the mix matches the composer’s stereo mix. To take care of grosser dynamic moves that involve the whole ensemble, I routed all the stems through a submaster group. In this way I was able to move through the mix and gently duck just the channels with musical activity that challenged the voice, leaving the pedal tones, legato chords, and such, chugging right along at a respectable level. In practice, it feels very much like conducting an orchestra.
Once the mixes were accomplished and a rough sequence was established, we printed a listen copy and sent it up the corporate ladder for the mixes to be approved, carefully including a message that the sequencing wasn’t complete and please ignore the timing of the spaces between sections because they would be set later. It works like a charm: the mixes were heartily approved but there were frantic communications passed down that the spaces between the sections were all wrong and needed to be corrected. Hehehe.
With content approval complete we moved on mastering, beginning with final sequencing, and leveling. Here it would help to mention that the score for this project is truly through-scoring. The composer wrote the score to help us transition from chapter to chapter and the music continues in many of those gaps. He sometimes dropped to a pedal tone and a pad in the breaks to make my editing easy, but the music did continue between chapters. With a normal music CD, you mix the tunes and send them as individual files to the mastering house where the mastering engineer sets the overall level of the project and then adjusts the song’s levels and density and the space between them so that they mesh into a single work that flows smoothly. By contrast, this project was very much like a live pop or rock music CD. With a live CD you have a continuous audience filling the gaps between the songs. You typically export the whole album as one continuous file (or two for vinyl) and then assign track start locations in the mastering software. With continuous music through this project, that is the approached I adopted. I mixed the entire CD, front to back, and exported it as a single file. Once we had a mix, I mastered for level and tonality, in this case working with -12LUFS as the density goal. Once we had a leveled product, I began adjusting transition times to finalize the sequence, tightening, or loosening, as necessary. With the sequence and levels finalized it was time to move on to CD mastering. I output a 44.1k, 16-bit copy of the complete mix. Once again, at this stage I either had to send the results up the corporate ladder for approval or have the executive producer on-site to approve the product.
Next, I moved my 103 minute, 27 second wave file into Steinberg’s WaveLab Pro 10, which is an excellent professional mastering platform that allows everything to be adjusted and all the technical details for the CD to be set. Technically, most would do ALL their mastering in the software, but I have become so adjusted to my DAW, Steinberg Nuendo, that I prefer to do the spectral and level work right there. The tools are the same. So, off we go to WaveLab. This program can output either a burned CD or a “DDP” or “Disc Description Protocol” folder, a collection of files that allows the CD plant to exactly reproduce my CD mastering via replication with a glass master for long runs. My first considered action was to set the markers for the sections. Each of these markers needs to be set in such a way that a CD player’s head will intercept the data stream and begin playback in a place that is as euphonic as possible. Frankly, it comes down to trial-and-error and taste. I sat with the executive producer and we chose start points that sounded nice. I burned a physical CD, and we double-checked the results on it. Over time you learn little bits of minutia such as leaving a half second at the beginning of the CD track that prevents CD players from up cutting the beginning of the CD and individual tracks and including a couple of silent seconds at the end to prevent the system from clipping the end of the track. It shouldn’t have to be done, but there it is.
And then, it’s the fiddly bits! The CD and each of the tracks will carry metadata so that no matter how they arrive at someone’s player, the album name, artist, track title, and copyright declaration follow along. The mastering company will take this information and enter it into Nielsen’s Gracenote Inc. database so that it shows up in Media Player and iTunes if the CD is played on a computer or ripped. You can also enter an ISRC code and UPC/EAN code to support retail sale. The Red Book CD Standard allows the possibility of embedding CD Text into the metadata so that a CD Text-capable player will display the artist, album, and track titles. You enter all this poop, and the program includes it in the DDP folder in the appropriate files. It is all very fiddly indeed, and there is a certain amount of legal specificity required to protect everyone’s rights. I like to include the CD-text because it is a little treat for the artist when he first plays the CD. In another section, you assign the project an identity in one of the files and a contact point and phone number are provided there as well. In this case, I made the contact point myself and provided the studio number. There really aren’t any technical types to handle technical questions in the client’s organization, so I have the plant call me.
Once you get everything correct, you burn listen copies so that the product can be tested by those up the client’s corporate ladder. When the approval copies are dispatched, the waiting game begins. At each step you have attempted to convey to the client’s leadership that these steps are “gates,” that the decisions are cascading ones. From each approval gate forward, if a reviewer has an objection to a characteristic that was previously approved, you will likely have to trash a bunch of work, move backwards in the decision tree, and start from a location where the desired change can logically be made. Then all the work from that point forward must be redone. Typically, because these projects are up against a deadline, capricious changes can be warded off by informing management of the time consequences a change will cause. Still, there are times when someone hasn’t really been engaged in the listening process and suddenly hears something he doesn’t like, way down the production path. I dislike doing the same work twice, but this is a service profession. I provide the requested service and do it cheerfully. In this case the clients handled the decision-making process logically and we sailed through.
Finally, when all approval had been given, I exported the DDP folder twice and compared the result to make sure they were identical and complete, doubled-checked the contents, and then FTP’d the folder to the fabricating plant’s site. Simultaneously, the graphic artist was sending his or her files so that CD, label, and container could be printed and fabricated in one run. Once my part was done, I went home to enjoy the rest of my day.
But before plant production can ramp up, a normal checkout process must happen. Within a few days of receiving the DDP, the plant sends us check discs which have been generated by creating the glass master and fabricating a short run. This is an actual production disc. I review my copy on a designated CD player that I have used to review check discs for years. It has become the standard. If the CD works, as in plays through and allows proper accessing of the tracks, I send out a report and the fabrication begins.
And what project is completely without an abnormal but hilarious circumstance: A couple of hours after I went home, I started receiving a barrage of frantic texts, phone calls, and emails from my client. The plant had contacted them and informed them that they were missing the data they needed to fill out the Gracenote form. My client(s) frantically contacted me. I got a clue right off the bat that something wasn’t right because the IDENT.TXT file within the DDP contains half of this information and lists ME as the contact point. They had not contacted me. Think on.
Nevertheless, I rushed back to work and checked things out. Yes, the data were all there and the project identity files (including me as contact point) were present in the DDP. So, I called up the plant manager and asked about the problem. He wasn’t sure what was wrong, so I asked to talk with the process technician who had generated the error message. Within a few seconds I was speaking with the guy responsible for the fabrication of this CD. He said that the Gracenote data wasn’t available in my folder. I asked if he had checked the files for that info because the data points were all there. He said no, but that he preferred to have all the data in a readily accessible text file. He told me the data he needed, and I agreed to immediately export a text report containing all the metadata and FTP it to him, pronto. We got off the phone and I created the file and sent it. There is an option in the WaveLab software to export this info in a nicely formatted HTML file, but I just typed up a text file per his request. I called the technician back in ten minutes and asked him to quickly load and check my text file. He was delighted that I had gotten back to him so soon and loaded and approved the information. I sent a calming email to all concerned showing the steps I had taken and the people I had contacted. All the participants up and down the corporate ladder were pleased, and the process was able to go forward. Voile’!
I expect the check disc to arrive Monday and we will review it. In the decade I have been working with this plant I have only had one faulty check disc so I expect the production run will begin sometime next week. Meanwhile, I formatted and exported the audio files for the streaming release at 48k and 16 bit. I delivered them to the producer who will oversee posting them online for streaming. Lord willing, all I have left to do on this project is to approve the plant’s check disc.
So there you go: Soup to nuts on a CD production experience.
=
=