Session Files: Restoring a Little Piece of History.
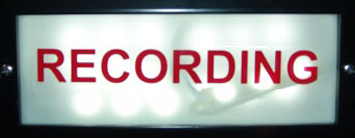
The other day I had one of those unique experiences that only come around once or twice in your career but leaves a strong impression. Knowing that I have experience in restoring archival recordings, a friend who collects unique and rare recordings asked me to resurrect a rather historical 1/4" tape recording that dated from the beginning of the 1970s. After examining the tape I told the client that he had a really historical piece in his hands and that I didn't want to take any chances with the master tape. We would need to go slowly. I could see some tape decomposition on the raw end of the tape so before we did anything else, I took a tiny sample of the end of the tape into the shop and tested it to make sure the backing was polyester rather than acetate. I did this even though I had a pretty good hunch it was polyester from the date of the recording. My method was to hold the specimen in a pair of pliers and heat it with a heat shrink gun, exposing it to temperatures over 300 degrees as measured by a laser thermometer. Rather than beginning to combust, the tape deformed a little, making it clear that this tape had a polyester backing. It was imperative to establish that fact so that the next step of the archiving process wouldn't damage or destroy the tape.
WOULD YOU LIKE THAT REGULAR OR EXTRA CRISPY?
That next step was to “bake” the tape to prevent oxide shedding. This step is necessary because of a common failure in tape design towards the end of the twentieth century. Unknown to the tape designers, the adhesive or “binder” used to glue the oxide to the backing was “hygroscopic,” meaning that it absorbed humidity from the air around it. Over a period of time two things would typically happened: The adhesive would become soft and began to ooze and the oxide, the material that carried the recorded signal, would begin to flake off. Both of these actions could be fatal to the tape. Oxide shed would cause dropouts in the signal. Large sections of oxide could actually detach and re-adhere to another place in the tape causing a thump. When the binder oozed, it adhered to the tape machine’s heads and tape guides. Shed oxide would then build up on those stationary parts of the machine, causing friction against the tape. At the minimum, the tape would begin to exhibit “scrape flutter,” a horrible squealing fluttery sound. At the worst the friction would bring the tape to a screeching halt and possibly cause the tape to snap. When we first began discovering the phenomenon in the 1990s I experienced tapes that would run no more than four or five seconds before the glue and oxide built up on the machine and brought things to a halt. The result could be a ruined tape and an hour of sticky, goopy machine cleanup with isopropanol and cotton swabs for me. There have since been studies by the tape manufacturers that established the causes of the phenomenon and prescribed its cures. These days I won’t even put up an old tape without baking it to remove the humidity from the binder and stabilize the tape. In some cases with multitrack masters I send the tape off to a lab where it is both baked and bathed in a chemical treatment for best results. The lab returns the tape in a hermetically-sealed bag with a warning to play back and transfer the contents before thirty days elapse because the stabilized tape immediately begins absorbing moisture and will return to its unplayable state. In this case the tape was placed on a cardboard sheet and baked for ninety minutes in an oven that had been pre-heated to 120 degrees. After baking, the tape was allowed to cool in the oven before it was removed.
Next it was time to bring a distinguished visitor into the studio.
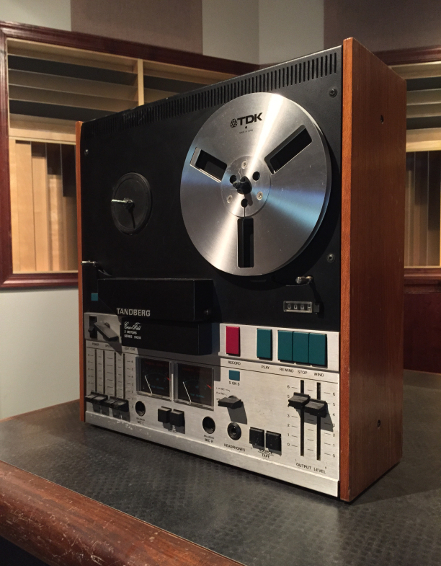
Click pics for larger versions
Meet the Tandberg 9100X, a Norwegian-built tape recorder that dates from 1976. Tandberg was considered the epitome of consumer tape technology in the 1960s and 1970s. This machine features “Cross-Field Recording” that allows a higher signal-to-noise ratio than most other designs. It accomplishes this by adding a second recording head that swings up to the back side of the tape when you hit record, and imposes a 180-degree out-of-phase magnetic influence on the tape. This allows a deeper magnetic penetration into the oxide, and thus a higher signal before distortion. Since noise from a tape is a constant, any increase in the recorded signal strength increases the distance between the noise and the signal! The Tandberg units had AC induction reel motors and a servo-controlled capstan motor, just like the big guys. They had a microprocessor-controlled transport that offered extremely smooth tape handling that was virtually fail-safe. On Spring break in 1977 my friend Gary Helrigel lent me his gorgeous 9100X to play with. For a week I used it to do my first serious experiments in recording as I was considering becoming a recording engineer. Thanks, Gary. I guess you could say I have a soft spot in my heart for this tape deck model. This particular unit is a survivor of the 1970s that I picked up for pennies at a studio fire sale few years ago.
TRANSFER
After digging it out of storage and bringing it into the studio I plugged it in and fired it up, fully expecting it to go poof! and give up the ghost immediately. Au contraire, Pierre, it worked perfectly like the trooper it is, and off we went on the restoration. The next step was to mount the tape on a last-generation Sony APR-5003 pro 1/4" tape deck and perform a slow packing wind, first onto a takeup reel and then back to its own reel, to create a proper pack of tape on the reel before we attempted a trial playback. A quick check established that the tape was holding up well. Many pro decks such as the Sony offered a slower, more consistent, winding mode called “pack mode.” The idea is to even out the windings so that this fragile, forty-four year old tape won’t be subject to any extremes of pressure as we began to play and shuttle it. Next I connected up the Tandberg tape deck to the mixing console using a pair of direct boxes to change the high impedance consumer signal to low impedance. From there the signal went to our digital audio workstation that runs with Steinberg’s excellent Nuendo software. I found a nice, loud passage, balanced the channels, set the console level at 100%, and then transferred the tape without manipulating the levels at all. When I finished the transfer I carefully moved the tape back to the Sony pro machine and packed it onto its reel again. I sealed the reel and box into a bag while it was in our machine room's low-humidty atmosphere for archival storage.
MASTERING
Next we moved into the mastering phase. First I experimented with various settings in iZotope De-Noiser plugin to remove the tape hiss and system self-noise. With a bit of tweaking we had excellent results, but in the end we decided to maintain the recording as a direct transfer without any EQ, noise reduction, or compression. That's how good the original and the transfer were. The one bit of processing I affected was to use a click-removal plugin to get rid of a static-induced spike in the recording. I isolated the section with the spike and applied the iZotope De-Clicker plugin to that zone only. From there I simply normalized the recordings and transferred them into Steinberg Wave Lab to be formatted as a CD. On the original tape the introduction and end comments were set apart from the body of the program by the program’s original editor, presumably because of the historical value they represented, so I maintained that formatting but I kept the musical performance by the recording artist as a solid, continuous program. I followed the standard procedure for live albums, placing cue points at the beginning of each song (after the introductory remarks) so that once the listener gives the program a listen-through in its entirety he can jump to a song of interest without a long introduction. I added CD and track metatdata within WaveLab and generated audition copies for the client.
AND THE TAPE?
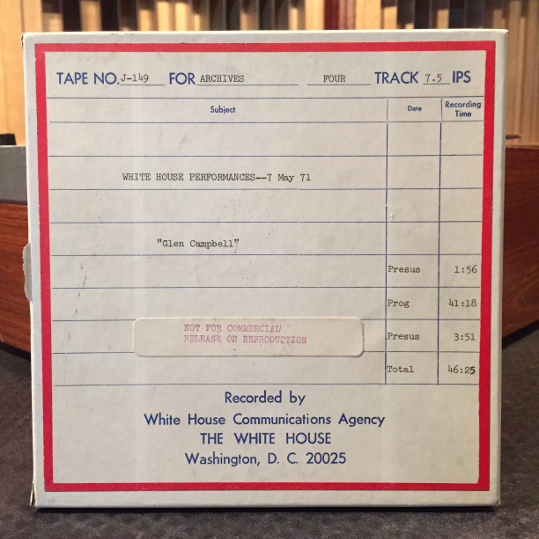
Oh, yes. Well, let’s see. Holding this tape in my hands for the first time I got a little shiver down my spine and one of those feelings, you know, “Wow, this is the genuine article. I am literally holding history in my hands.” This is the only known copy of a White House Concert held on May 7th, 1971, a “Salute to Agriculture Reception and Dinner” featuring entertainment by a very young Glen Campbell at the peak of his career. There are pictures from the event that have left Nixon historians and Glen Campbell aficionados alike scouring the archives to find this recording. This year, forty-four years later, this copy surfaced. This high-quality dub was made and cataloged for the White House Archives. The box has the “White House Communications Agency” label that tells me that it was recorded by the organization originally set up by Phil Ramone in the 1960s. Ramone had attended a musical performance put on by the White House during the Kennedy administration and had been dismayed to find that the sound reinforcement was dismal. A short time later he was invited back by Kennedy to work with his administration to improve the quality of White House audio productions. Phil set up the agency and worked with it during the Kennedy, Johnson, and Carter administrations.
I’m sitting here right now doing the transfer in real time, listening to a performance that probably hasn’t been heard since the 1970s. Let me tell you, I can hear the influence of Phil Ramone in this recording. It is state of the art for the period, with clear, open, noise-free sound and a good mix of the instruments and vocals. We’ve heard President Richard Nixon introduce Glen and mention that First Lady Pat actually first suggested Glen as the artist for the evening. Glen has played a six-string, a twelve-string, and an electric classical guitar with a very early piezo pickup in it. He and his band have done most of his hits of the period plus some other current tunes including Roy Orbison’s “Sweet Dreams Baby” and “Classical Gas” by Glen’s friend, Mason Williams. Having been raised on a farm, Glen sounds completely at home cracking farm jokes between songs. At the end we hear Glen and President Nixon trading off-mic salutations as the applause dies out and then the comments from each of them that close the performance.
And there is another one of those delicious, serendipitous little ironies involved in this archival process. Once I got the tape mounted and began playing it back I was amazed at how well the recording was reproduced by my tape deck. Usually there are little EQ differences that creep in when you record the product on one brand of tape deck and play it back on another, even if both brands are using the same EQ standard. There can even be differences between two recorders of the same brands if they’ve been tweaked. As a result, a transfer of this kind usually requires a bit of EQ adjustment to restore the recording to a natural sound. However, this transfer required literally no adjustment and yet sounded marvelously natural and open. That so rarely happens that it got me wondering, so I went out and did a little research on the web that yielded a fascinating discovery: As it turns out, somewhere along the line the Kennedy administration began using Tandberg recorders for its consumer recording chores. This might have been as a result of Phil Ramone. Since this tape was made only two years after Phil left the agency, there is a strong chance that the tape that was handed to me was recorded on the very same brand of machine that I played it back on.
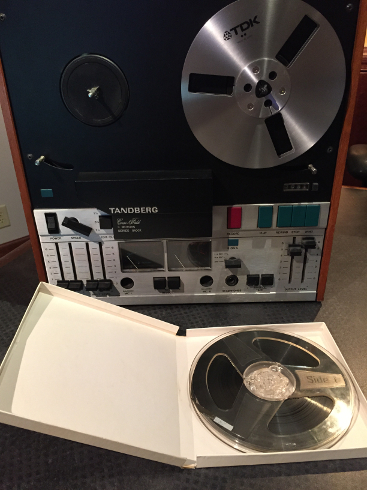
Whatever the strange twists and ironies of the project, it was a pleasure to be invited to supervise the project, to literally hold a piece of history in my hands, to be the first to hear this program in decades, and to finally be able to present back to the client a marvelous, clear preservation that will allow others in the future to experience this little moment in time.
=
=