A TOUR OF THE STUDIO WHERE I WORK
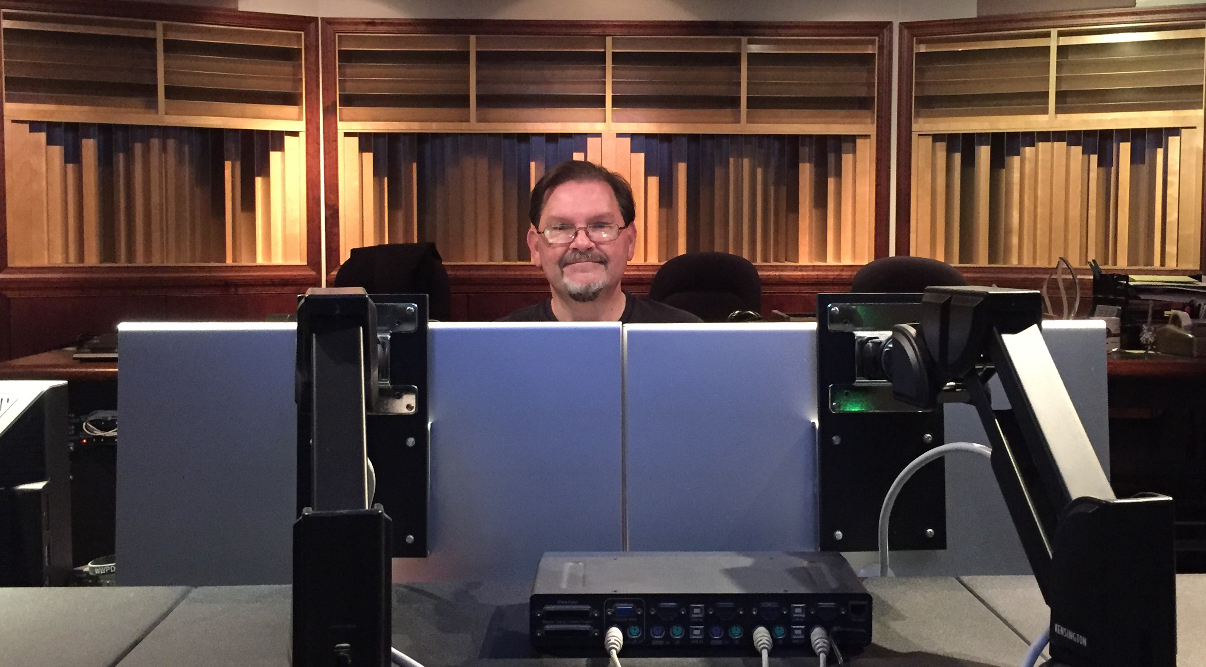
On one of the forums I frequent I was asked to post a photo tour of the studio where I work, so here we go. The official name of the suite is "Audio Post Production Suite One," though for some years it has been unofficially called "Bob's Room." It is a combined recording studio/post production Suite, one of three in the complex. When I joined the company many moons ago we began working towards the realization of this room as the premier suite in the house. Fifteen years later, in 1996, it was finally completed. Leadership asked that it be built state-of-the-art so we sent a designer to Syn-Aud-Con to study Chips Davis' Live-End-Dead-End (LEDE) design principles. He came back and designed this space, including an (unlicensed) LEDE control room. This design features rigid walls with dead spaces and a shell that is designed to be as anechoic as possible in the front half and diffuse in the back half. The idea is to create an environment where the acoustic output of the monitors arrives at the mix position with as few reflections or secondary paths as possible in order to maintain phase coherency and proper spacial relations reproduction across the sound stage. Then, carefully managed diffuse return is added from the back wall in order to prevent the room from being too dead-sounding. A too-dead room encourages engineers to add too much reverb to their music mixes. This recording suite was built from the ground up within an existing building shell. Each room is built on a floated floor. Here is a detail of the multi-layer, 2"x2" rubber floating blocks. They were placed at twelve-inch centers in sheet fiberglass insulation upon which the pans for the floor slabs float. Once the pans were in place, the concrete floors were poured.
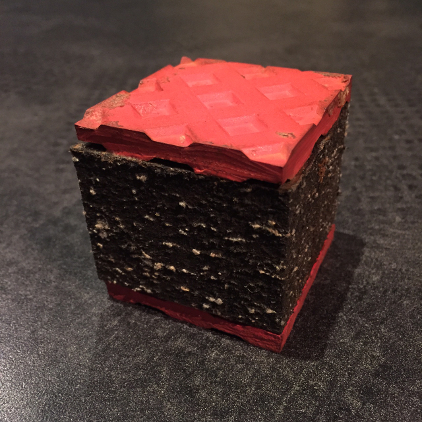
The wall assemblies around each room consist of three walls. Each of the three walls has its own wall studs and is built-up of three thicknesses of 3/4" sheet rock, glued and screwed togetther and to the studs and laid with seams overlapping solid boards for rigidity. The inside walls are built on machine rubber strips sited on the floated floors, the two outside walls are built on the machine rubber strips on the sub-floor. There are 18" spaces with absorbent mounted on one side between each of the three walls. The combination of rigidity and isolation increases sound attenuation and thus lowers acoustic transfer.
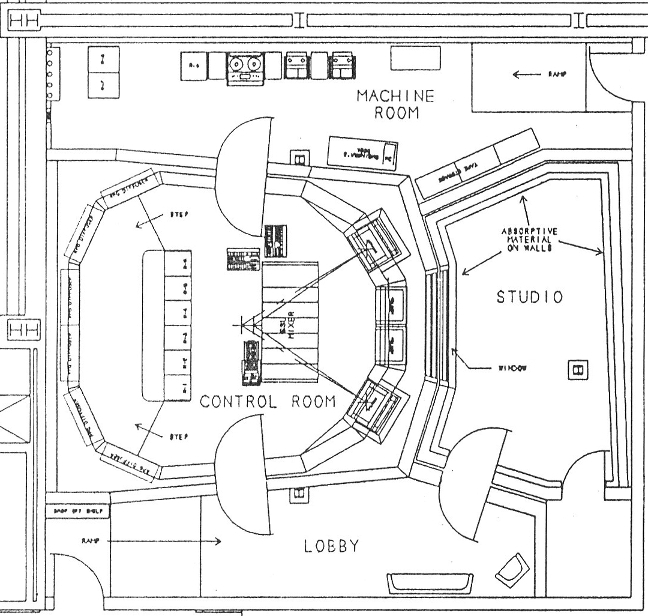
Custom-fabricated steel I-beam pillars support the main stereo monitors within the soffit. We had our construction crew excavate and pour sub-foundations below the concrete floor and the beams were bolted to them. Plywood boxes were built onto the pillars to carry the monitors at the proper angles to point the monitors exactly at the mix position. All of this isolation was provided so that vibrations from the monitors aren't transmitted into the foundation or walls and thence to the mix position. This is important because sound travels more quickly through a solid than though air and would thus arrive before the airborne output of the speakers, thus clouding the phase picture.
The recording suite consists of the control room, the medium-dead recording room, the live room/waiting room, a mic closet, and the machine room. So, let's enter and tour the suite.
Tucked away towards the back of the corporate studio building, behind a pair of double doors and a pair of heavy acoustic and fire-rated doors, there is a small lobby. In this lobby, the unmarked dark oak door to the left is the entrance to my suite.
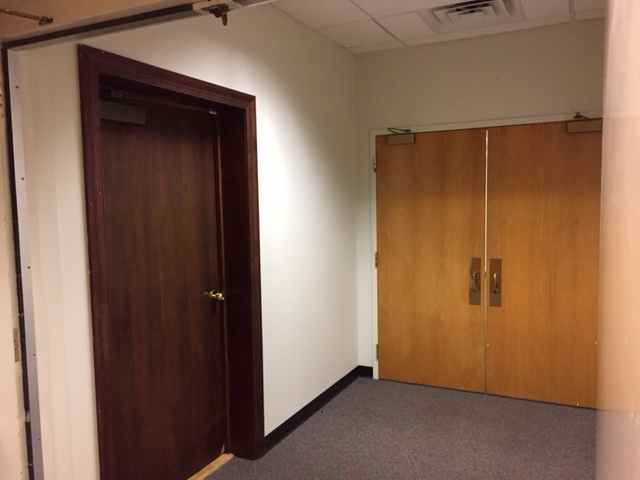
In the plan drawing above this you can see this door at the bottom-left corner. Step inside and turn right and you see the live room/waiting room. Note non-parallel walls and ramp up to floated floor. Direct work lights and indirect lighting for atmosphere are provided. There is a wall box with eight mic lines, four returns, video feed, and two headphone feeds built in right behind the structural pillar on the left, just beyond the first door.
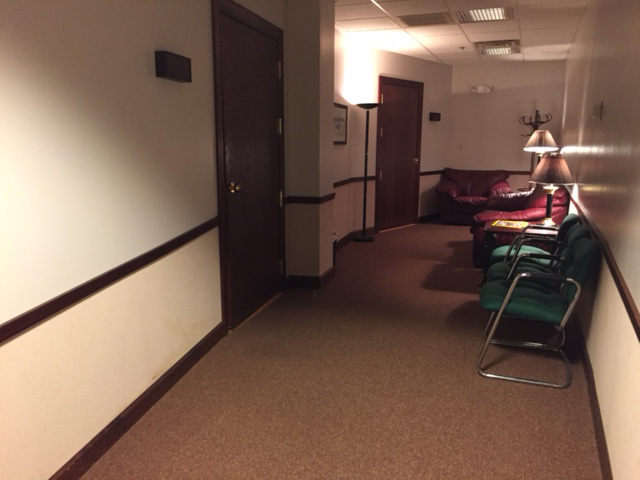
This room is great for acoustic guitar. I typically set up with the guitarist right on the sofa on the right. With some rearranging of the furniture you can fit in a drum kit. I've done vocals here as well. Guitar amps are GREAT here. You can space mics apart for room reflections or put the amp at one end and ambient mics at the other. The ambient SPL is 38db so the room also works well as a reverb room. Here is a typical application:
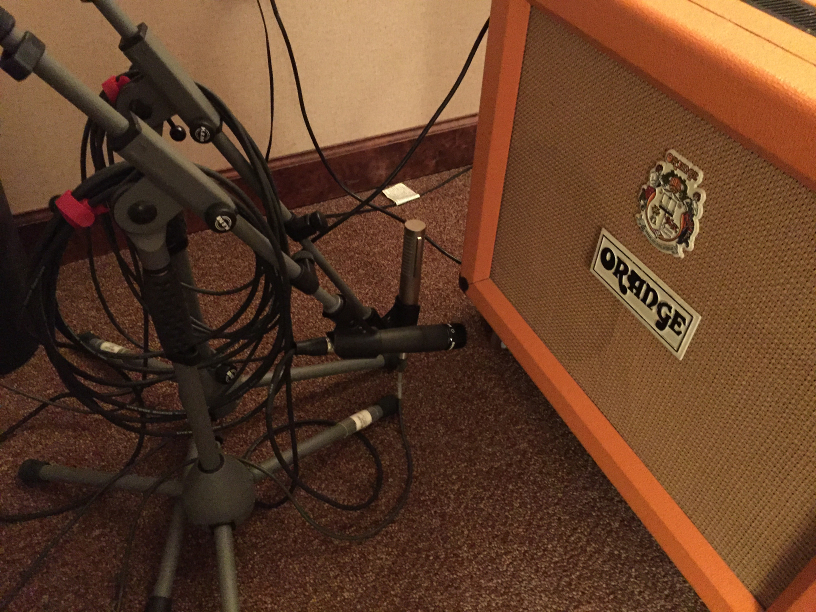
Inside the second door on the left in the picture of the lobby we find the medium-dead recording room.
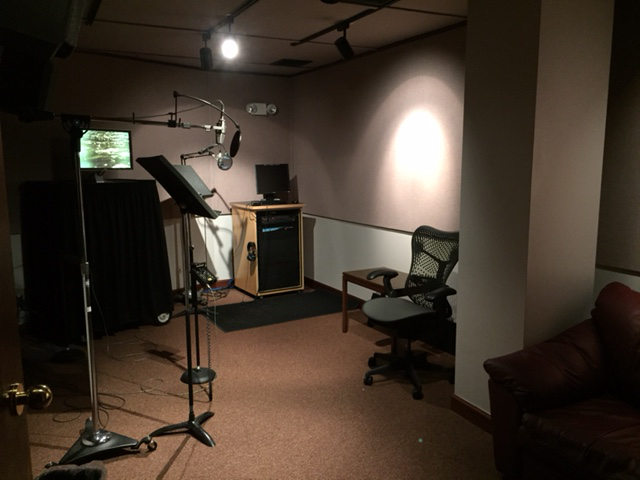
There's room for a LARGE drum set in here. I've recorded string quartets in there as well. A small ensemble is cozy. Voices are great here and there's very little problem with competition from room ambience. Two mic panels offer 24 mic lines, 8 returns, and 4 headphone jacks as well as video feeds. In the back corner is a self-serve recording system that allows voice-over talent to record themselves in the room if I am occupied with a mix in the control room. The ambient SPL is 38db.
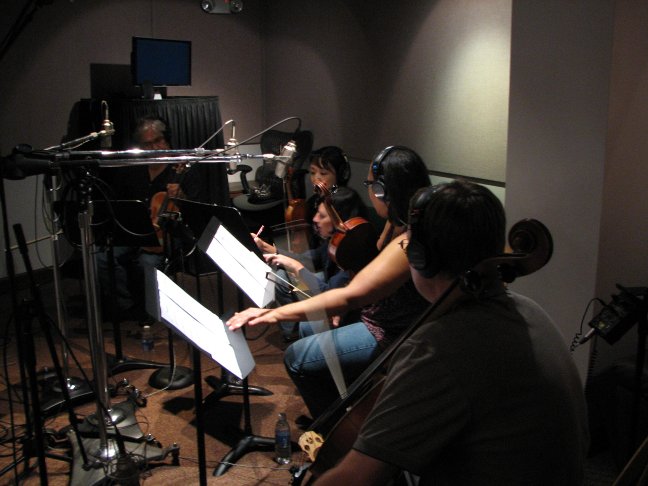
Step inside and turn to the right and you find the mic closet where stands, mics, cords and headphones live. Really, the mic library for the facility exists as small handfulls of mics in each of five studios plus a PA gear collection and a separate storage case with right about 250 mics, all told.
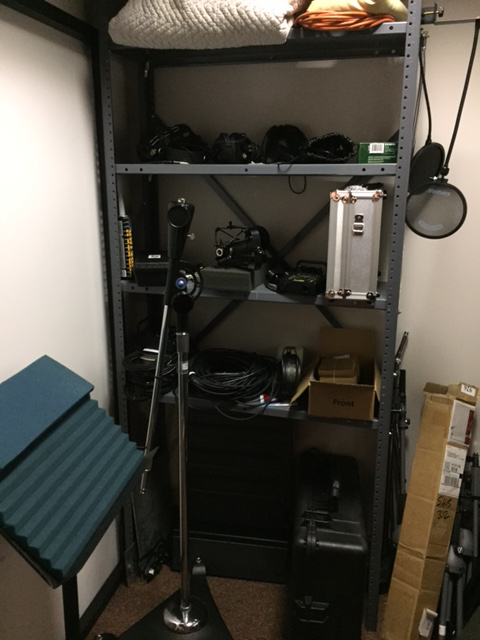
Now go back out to the live room/waiting room and open up the first of the two doors to get a detail of construction. Note the width that the three walls take up, the gasket filling the space between the casement halves to prevent shorting the inside and outside walls, and the solid oak double doors. Each door weighs 200 pounds and features a surround gasket and a mechanical sweep gasket on the lower edge that moves down and seals against the threshold.
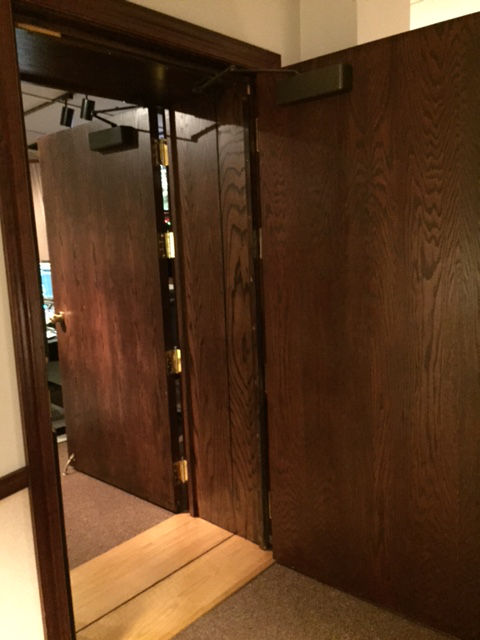
Going through the door here's the first glimpse of the control room. The front (dead end) is to the right. The machine room is dead ahead through the door with the window.
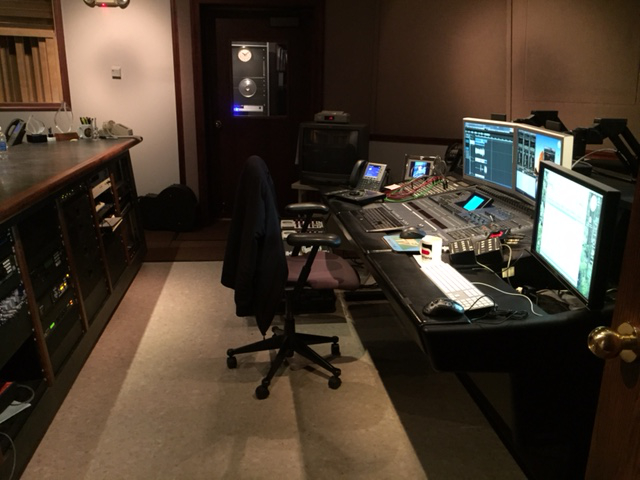
Here's a pic looking towards the front from the back of the control room. Note the square bezels over the monitors to the left and right of the studio window. They hide the Urei 813b/c monitors. Behind the console is the KRK 12S2 subwoofer that is paired with them The video monitor over the studio window is tied to the DAW.
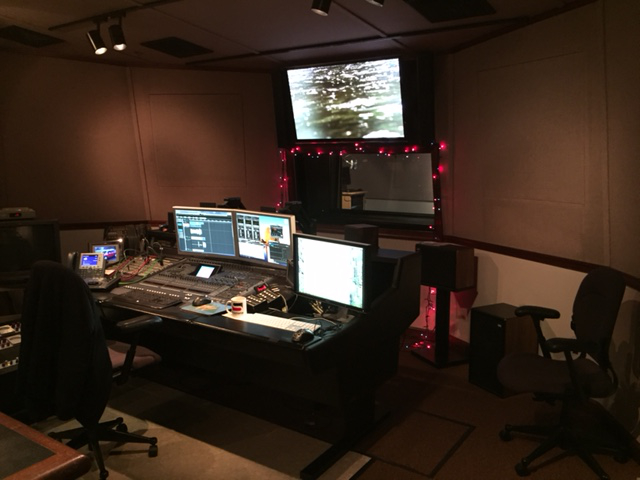
Here is a detail on the monitors.
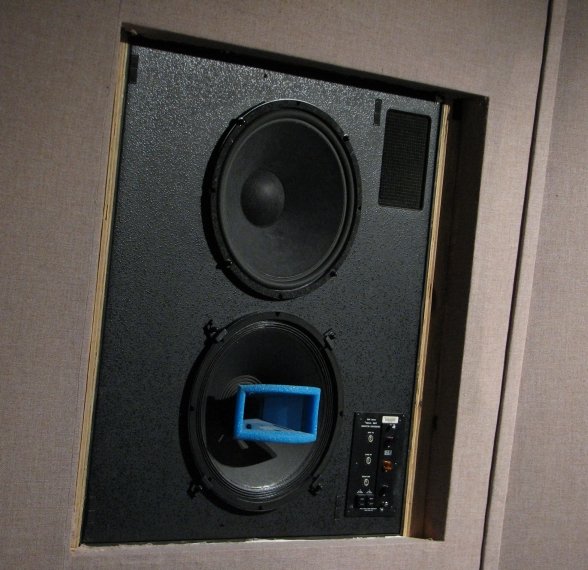
We've added a secondary array with networked JBL LSR4328P monitors and an LSR4312SP subwoofer.
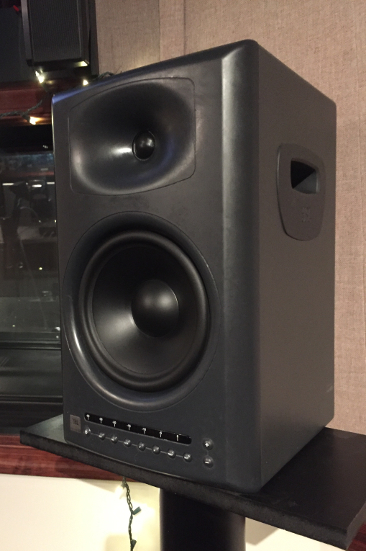
The surround array are Bag End MM-8s with D10E-L sub-woofers and ELF-M2 Low End Integrators. I hoist the front Bag End speakers onto pedestals on top of the subs when it is time to use them. Tertiary monitors are Auratones and TV Monitor speakers. My wife suggested I put up the Christmas lights around the holidays to add some cheer but everyone has loved them so much that I replace them during the years with white ones. There aren't any bass traps in this control room design because the non-parallel walled shell is designed to prevent the need. In measuring and tuning the rooms we found that the theory played out well into the practical because we found very little bass buildup in the significant listening locations and in the performance locations. The room EQs are set to be limited to six db of boost or cut. We are mainly using two to three db deflections in a couple of spots with one tab on one speaker more around four db of cut on the latest tuning, done a couple of months ago. The left-right sound field at the mix position is pretty nice without much comb-filtering as you move your head. There is good continuity as you move towards the ends of the console as well.
Here's a view of the back wall from the main monitor speakers. The diffuser panels were custom designed by Dr. Peter D'Antonio based upon blueprints of the room and were built by his company, RPG Diffusers. The producer's desk features mic panels on each end that are identical to the one in the live room. The rack looks a tad empty now that I moved the mic preamps to a turret rack to the left of the mix position and we've gone to mixing inside the box.
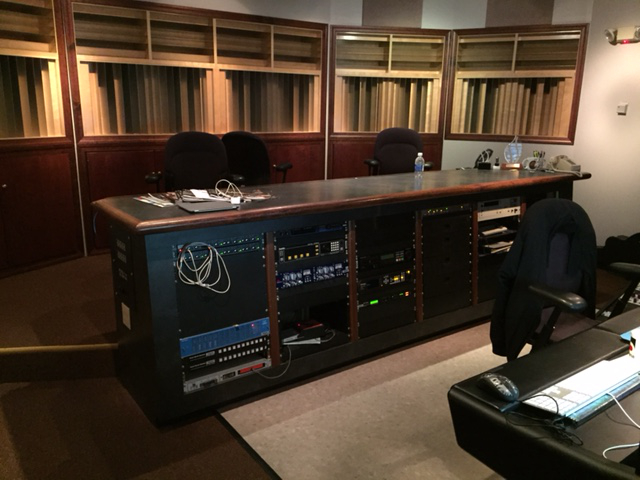
Here's a reverse view of the control room from the machine room door. You can see the turret rack at center bottom.
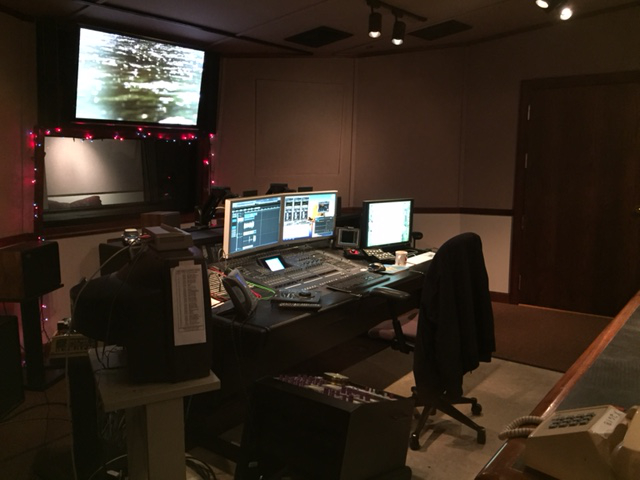
Here's a detail on the three-pane window and the depth between the two rooms. That's SIX walls and spaces, by the way. I can put a drum kit in the studio and there is no significant bleed into the control room. The ambient SPL is 40 in the control room.
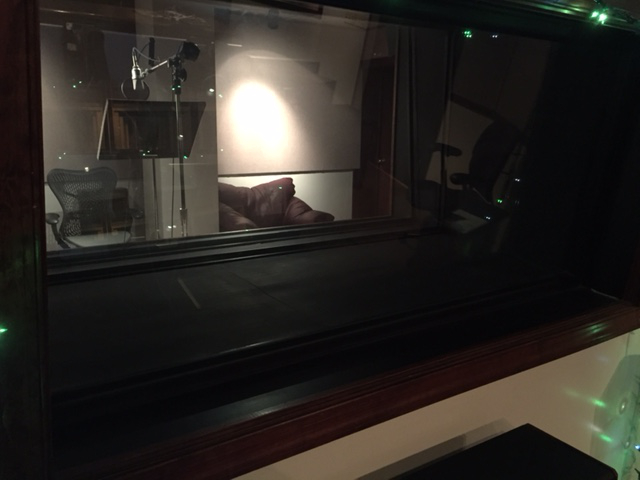
And just for fun:
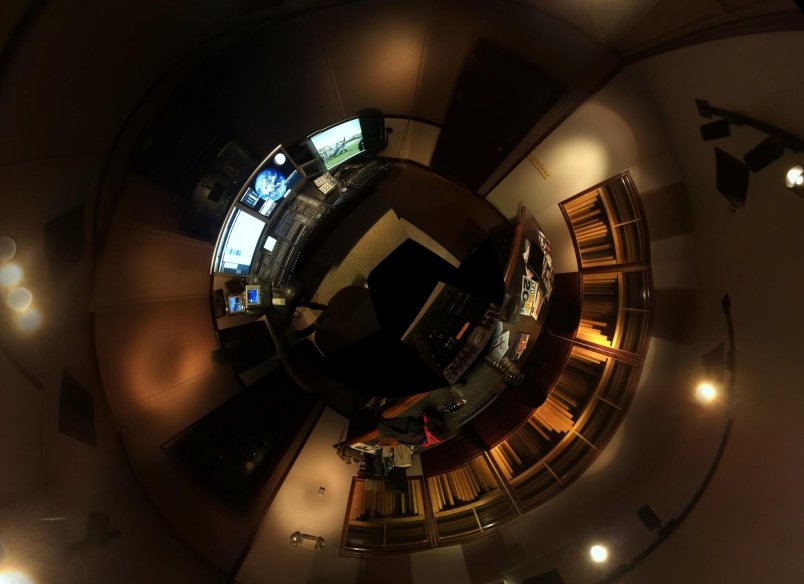
Here is a direct-on pic of my desk. Above the patch bay is a pair of Dorrough equal loudness meters that shows peak and VU at the same time. Below the patch bay is the Avid/Euphonix MC Transport controller with a large, weighted alpha wheel for transport control and zooming. There are soft keys for transport and editing controls. The two Mac monitors contain the GUI of the DAW. Above the window is a large monitor for video. The software is Steinberg Nuendo with several plug-in packs. We've got several Waves series, a UAD accelerator card with various plugs, a bunch of iZotope plugs, Antares Autotune, Drumagog, etc. The console is a Yamaha DM2000 96 channel digital box and is interfaced with Nuendo for fader and front panel control. The DAW keyboard is on the elbow pad in front of the console. To the right of the GUI monitors is the little DK Audio MSD600M metering device. It provides a display of phase coherence and energy from mono to stereo and up through 7.1 with a phase meter on the left, "jellyfish" display in the center, and channel metering on the right. It is indispensable for surround mixes and fantastic for quick phase info. There are monitoring controls below it and my personal engineer's computer on the right. The turret rack at lower left contains two Avalon tube preamps and one Neve Portico preamp. There's also a classic analog thermometer and hydrometer.
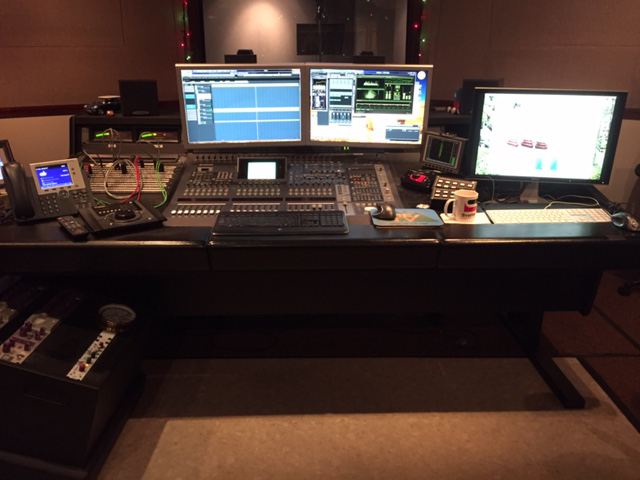
Turn ninety degrees left from the above shot and go through the door with the window and you are in the machine room. Everything with a fan (except the console) goes in here. This pic was facing left from the door. Since the room was built in '96, the gear has progressively grown smaller and smaller, freeing up space. The department storage has spilled over into here: processing gear, interfaces, preamps, power supplies, and storage boxes for many of the 250-odd mics we share between the studios, etc.
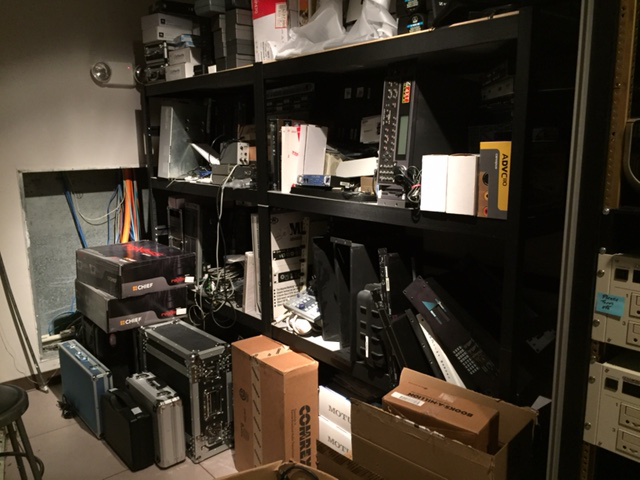
Turn ninety degrees to the right and you see the machine racks and the analog tape machines. That's a Sony (MCI) APR-24 multitrack with integrated Dolby SR noise reduction. Great machine, the final stage of analog high-tech. It stores three sets of biasing and EQ for each speed. A Sony APR5003v two-track sits behind it. We keep these machines to bring in legacy projects whenever they crop up. The last multitrack job was the remix of a soundtrack for album release. I've been doing quite a bit of archival digitizing of two-track masters as well. Note the damaged cone from my Gretsch reso now hanging on the rack to the left as industrial art. PC and Mac frames are below it. They are all connected to their keyboards, mouses, and displays, via extenders.
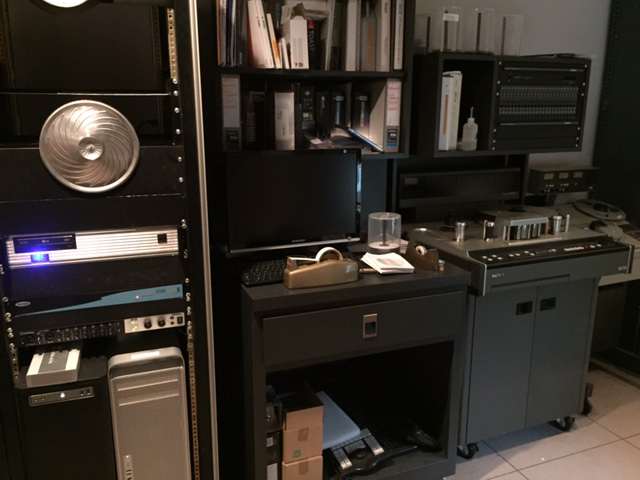
Another ninety degrees to the right shows my little office and the kitchenette at the other end of the machine room. All of the appliances are courtesy of my thoughtful wife. Note the RCA BK5B ribbon mic on the desk. I'm repairing its shock mount. The floor panels are concrete-filled for rigidity so they don't serve as tympanic sound transmitters.
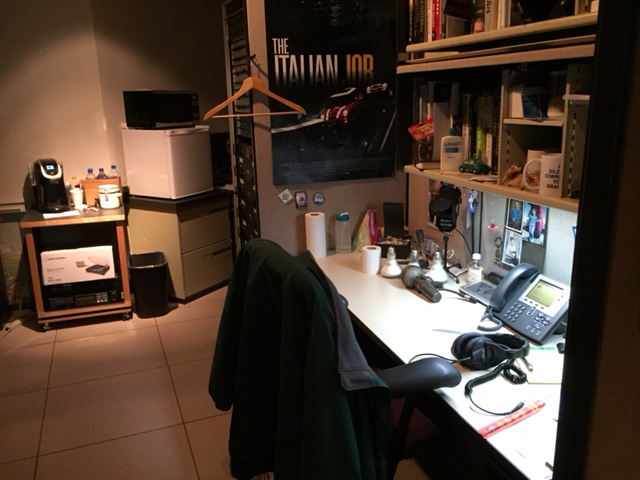
Down past the end of my office on the right is the amp rack. We've got David Haffler TransNova P7000 amps and Clark Teknik third-octave room equalizers for both main arrays. These are nice sounding amps! The mic stand is where I hang wet socks on cold winter days to warm and dry them in the forced-exhaust of the Hafflers.
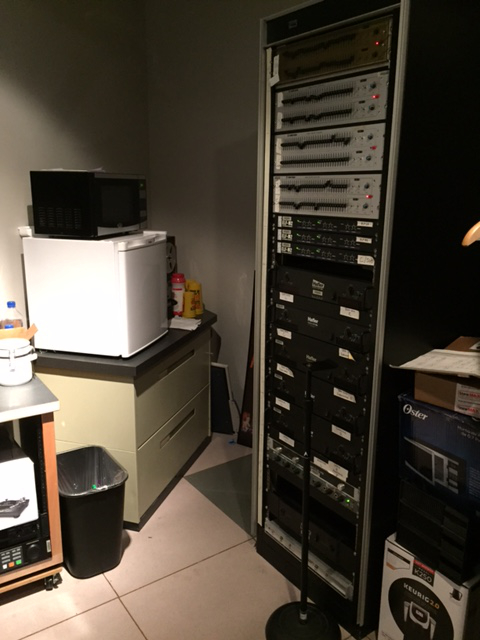
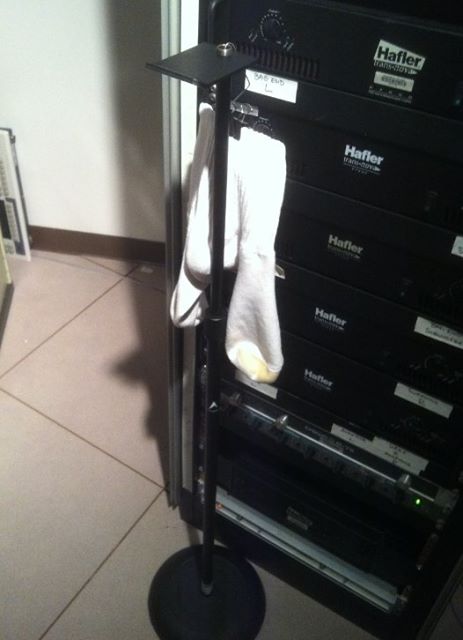
So there you have it. My little world. I am spoiled rotten, of course.
Oh, and a bit of history: When we opened the room it was centered around an SSL 4040E/G mixing console. We updated it to a 4048 (eight more channels) by the time this pic was shot in 2003. At the right-rear is the remote for the Sony 24 track. On top of the video monitor is a Dorrough equal loudness meter. In the modern pics above you can see that two of them are integrated into the new console. Oh, and I'm skinnier now.
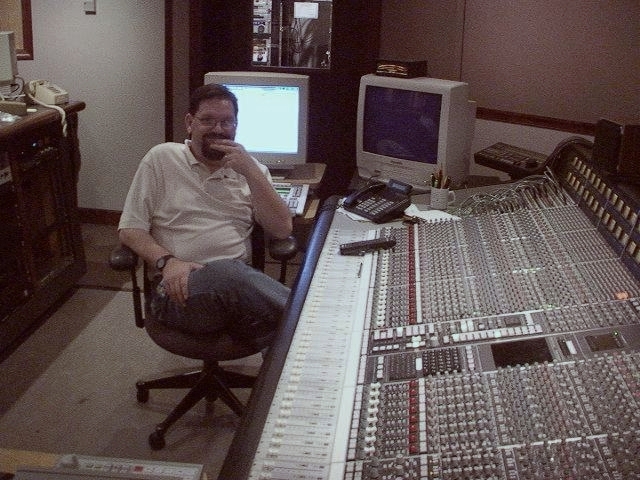
Below: Pre-Hi-Def days. The little green TimeLine Lynx remote on the right sync'd six transports. The bigger turret console at far right contained Dolby surround encoding units. Keyboard at left controlled a Fairlight MFX audio workstation. That's where I got my love of big, heavy alpha wheels. Oh, and my scheduling was still on paper at that point. The notebooks in the foreground contained the daily schedules and work orders for two shifts.
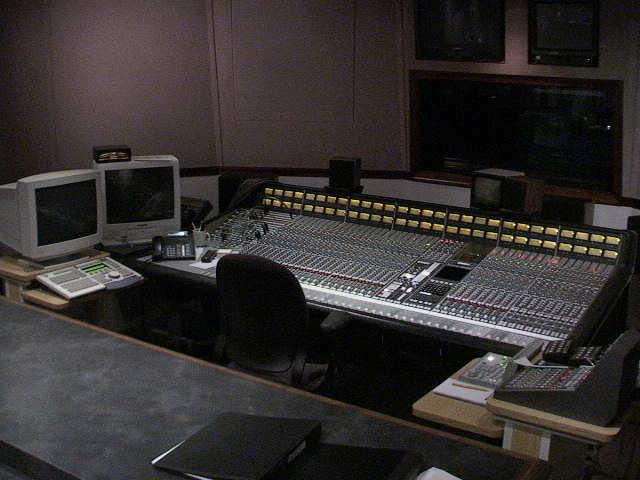
Mixing a Phil Keaggy performance right after the transition to Hi-Def video and a totally non-linear production flow. Still, a yukky flip phone pic. This would be about 2005 and note my same Svetlana Electron Devices mug as in the modern shot of the console!
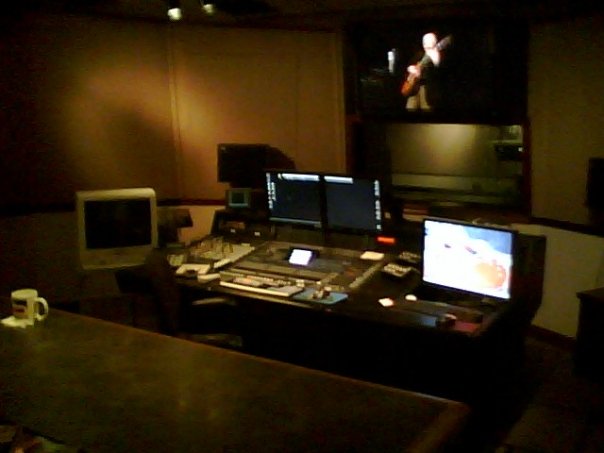
Since we've gone non-linear, server-based, and totally digital, the big console hasn't seemed necessary so we switched to the Yamaha. I miss all my knobs, but frankly, working inside the box is quite a bit slicker and exchanging product with the other four rooms is quite a bit easier. For instance I can move to another studio, access my project from the central audio server, and record grand piano if I need to, or I can take over only part of a mix, say dialog cleanup, foley, or music mixing, on a long-form job from another room.
Some specs:
1. The absorptive product we used to surface-treat the medium-dead recording room and front (anechoic) shell of the control room is two layers of three-inch thick Owens-Corning 703 fiberglass. The fiberglass is covered with speaker grille cloth. We actually found a company that specialized in installing these fabric walls. Dual layers of O-C 703 are also used on the center of each shell's three walls to reduce transmission within the walls.
2. The rubber block in fiberglass suspension system for the concrete floor pans was Kinetics RIM-L-2-12 roll-out isolation mats.
3. The walls are built on 1/4" machine rubber boots that rest on the floated slabs.
4. When I checked the plans I saw that the triple shell for each wasn't reduced at the meeting points.
5. The overlapping joints are back-filled and caulked with non-hardening acoustic caulk.
6. The three panes of glass between the control and the medium-dead room are 3/8," 1/2," and 3/8" Amerada Acousta-Pane 36 Sound-Rated glass and are splayed at three different angles and mounted in neoprene glazing channels.
7. HVAC: We had a custom high-volume, low-velocity system built with interior absorptive to reduce noise. The supply enters each of the rooms via its own labyrinthine absorptive box so that sound isn't transmitted into or out of the structure or between the rooms via the HVAC system.
8. Track lighting is furnished twelve volts. The original 120v systems caused both acoustic noise and induced hash into the power system when dimmed so we rewired with a twelve-volt transformer and use sealed quartz lamps.
9. The entire complex is on an uninteruptable power supply featuring a interim battery continuity supply and the engine/alternator from a diesel-electric locomotive that kicks in automatically and can run for more than a week. The power is also conditioned to remove ripple and spikes.
10. Fire suppression is via a water sprinkler system. During a dump, the system cuts the technical power supply to reduce risk of equipment damage. Several of the spaces in this complex are halon protected but EPA regs have made it necessary to procure that from overseas so this room was spec'd as water protected. I wasn't happy, but we've never had a dump.
11. There are two 20"w x 12"d cable channels built into the control room design to carry cables from console to rack and both console and rack to machine room. Cable access to the recording rooms is via conduits to reduce acoustic spill.
12. Besides conduits, the soffit video recess is fed its own air conditioning feed to prevent monitor and electrical gear from overheating. It was originally installed because the monitors were CRTs but has still proven useful in the flat panel TV monitor world. We've got a monitor amp up in there right now for the TV monitor speakers that has nothing to fear from heat.
13. In the back of the control room there are four covered boxes above the diffuser units that hold the surround monitors.
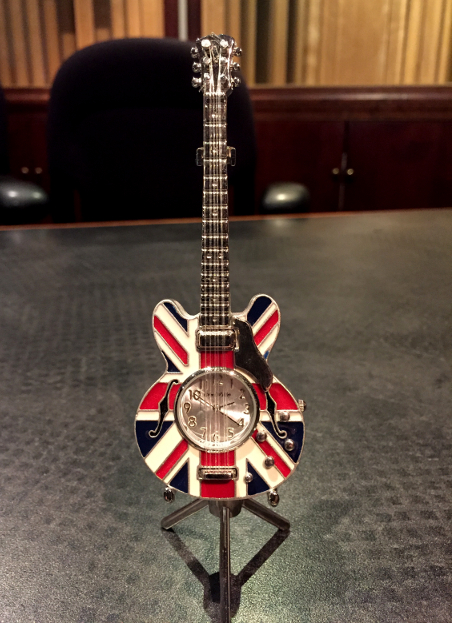
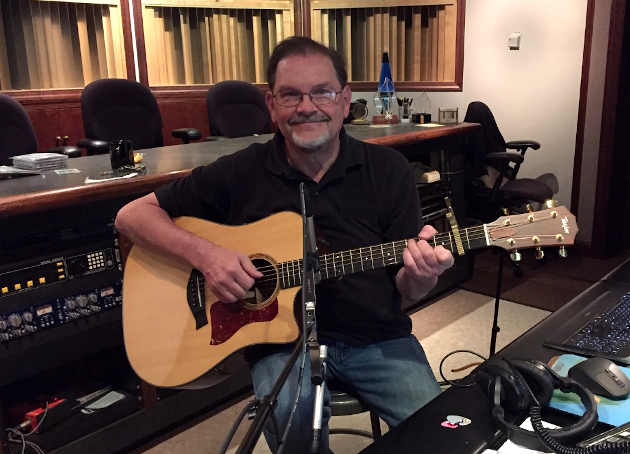
=
=