Reviving An Old Analog Friend
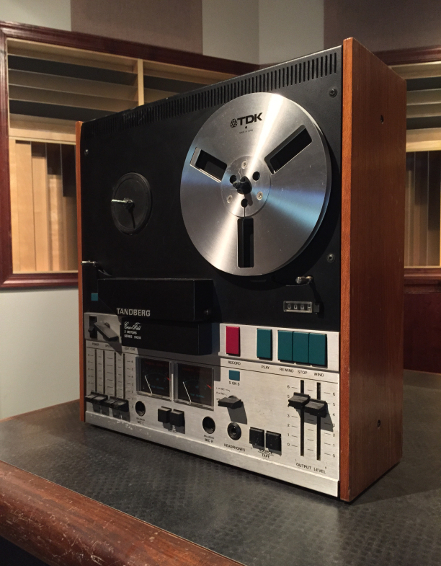
Tandberg 9100X Crossfield Recorder
Gather 'round kiddies and I'll tell you a tale,
of a fifty-year-old tape deck and parts in the mail.
04/15/2025
THE MACHINE
Over the past few days, I’ve been working on transferring some old audio tapes from the 1970s to digital files. To do so requires some unconventional gear, namely my personal Tandberg 9100X tape recorder. This recorder was built in Norway, sometime between 1974 and 1977. It uses the consumer quarter-track format on quarter-inch tape and accepts seven-inch reels. Interestingly, it offers what is known as the "Crossfield recording system." The final limitation on signal-to-noise ratio with tape was always depth of magnetic influence in the magnetic substrate on the tape. The deeper you could influence the magnetic particles on the tape, the higher a signal you could print on the tape without saturation. Since background noise is a constant, any increase in clean signal increases the signal-to-noise ratio. Tandberg came up wit the idea of using a second record head that swung up to the back of the tape and transduced a 180-degree, out-of-phase field to record more deeply into the tape substrate and allow recording of an increased signal. This unique deck features that Crossfield system.
In 1977, a good friend of mine loaned me his Tandberg 9100x deck over Spring break and I did my first really serious recording experiments on it. Then in the 1990s, a radio network was ceasing operations and I found this example of the same model in their fire sale for pennies. Despite its age, this one was nearly complete and completely functional except for missing its supply reel lock. Because of this, the machine had to be operated lying down or the supply reel would jump off and distribute its tape abroad. I considered that to be a small price to pay for securing an excellent tape machine in such good shape at such a low price. To properly play consumer-format tapes you need a consumer-format player (Um... duh?), so I’ve kept this deck in the machine room at the studio for just those occasions. Probably the most notable job I've done on the Tandberg was restoring and transferring the only known tape of 1971 Glen Campbell concert in the East Room of the White House. Yes, THAT White House.
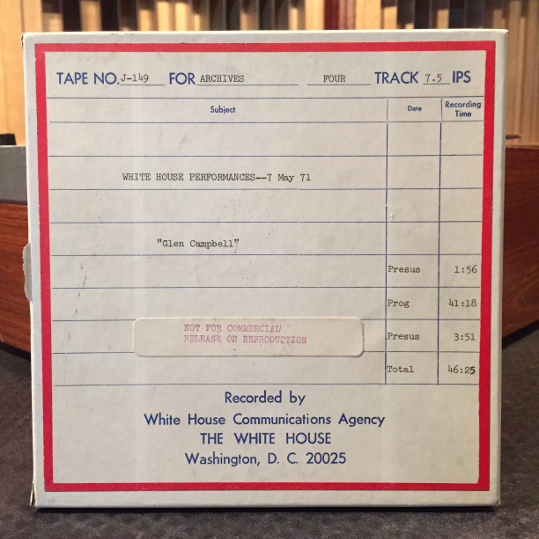
Because the White House used Tandberg tape decks in this period, I was glad I had the same brand of tape deck to reproduce this historic tape. More on that, HERE
But more recently, a client brought me a box of corporate recordings from the 1970s and asked that they be transferred. On day one of the project, I was delighted that the Tandberg fired up once again and performed flawlessly through a day's worth of transferring after sleeping for a half-year. But on day two, something was wrong in Denmark (Norway?). The machine’s pinch roller quit swinging up to pinch the tape against the capstan and get the show rolling. I found that if I gently swung it up manually, the solenoid that normally did that job at least had enough gumption to hold the pinch roller in place. Using this method, I was able to finish that day’s work, but what of the next one?
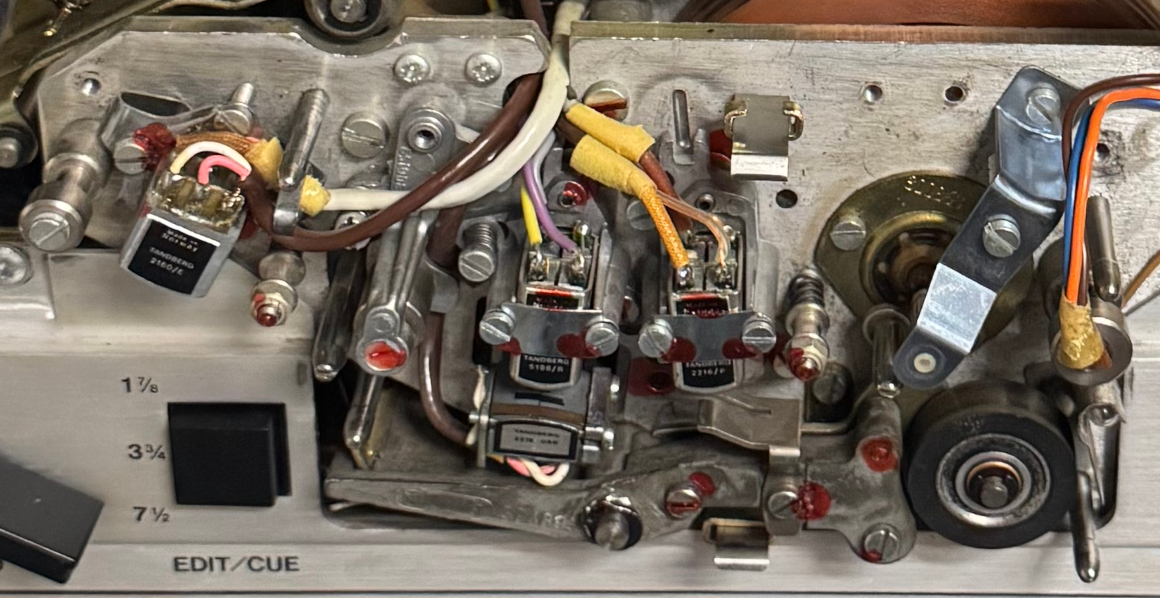
The head stack. Notice the Crossfield recording head opposite and below the center record head.
REVIVAL
On a hunch, I took the beast over to my friend David in the engineering shop on Thursday, described the issue, and confidently left it with him. David is the resident transport specialist here at the studio. He’s been working on tape transports of all types since the ‘70s and knows a thing or two. On any given day you'll likely find one or another electro-mechanical device pulled apart on his bench, being brought back to life by his gentle minstrations. I checked back the next morning (Friday) and stepped in just after he removed the machine's dress covers. Here’s what I saw:
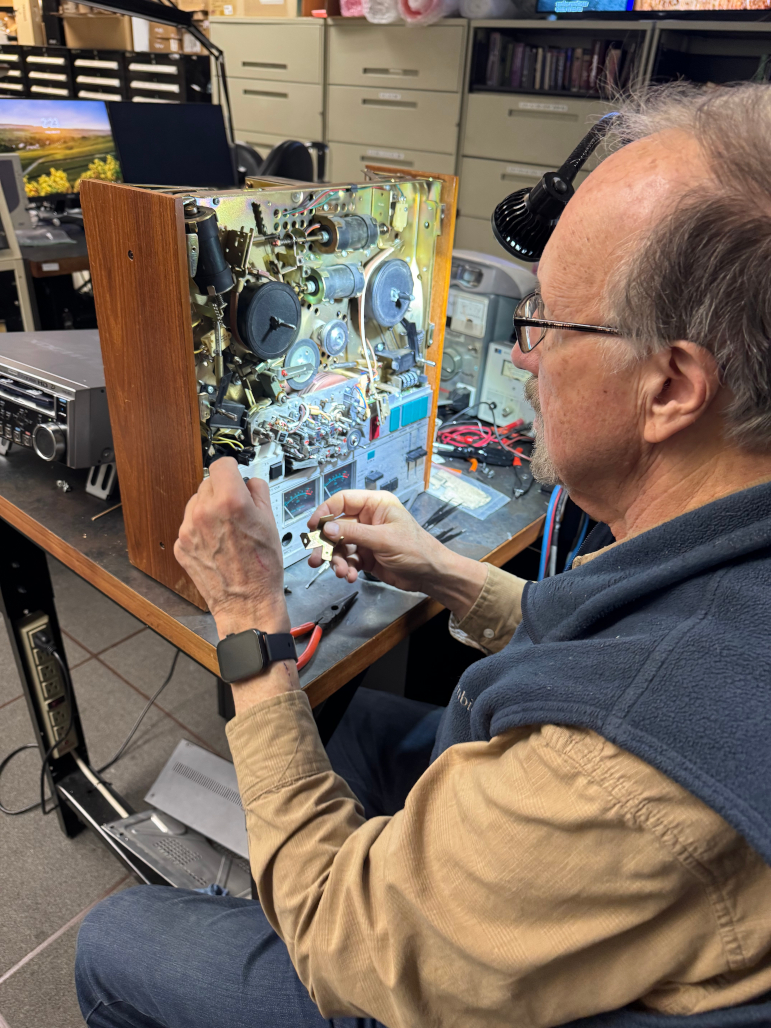
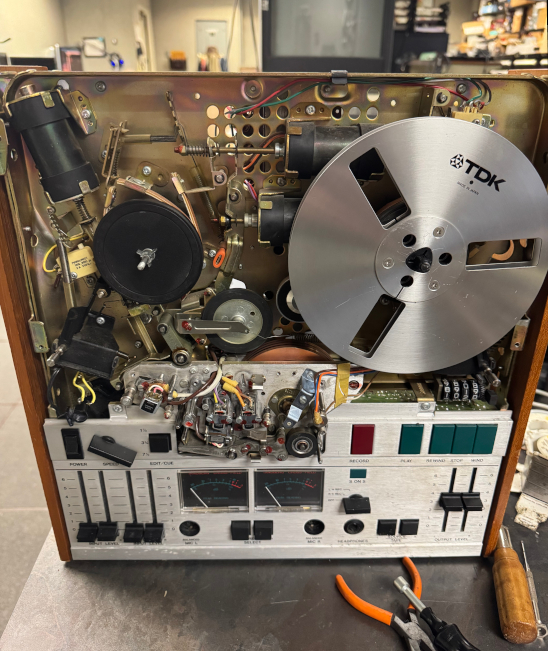
David started at the pinch roller swing arm (middle, right above the meters), finding that the years had led to a buildup of crud on the axle it swings on. He removed the circlip that secured it and gently eased it out enough to clean that bearing area. That made the arm swing more smoothly but didn’t fix the problem. Next, he cleaned the solenoid plunger that pushes up the arm and causes the pinch roller to pull the tape into contact with the capstan. The solenoid is the black can on the upper left of the chassis. The arm moved much smoother, but we were not out of the bushes yet. He traced the wiring from the solenoid to the “PLAY” switch logic board around back and found a connector array on the bottom left, just below a pair of relays.
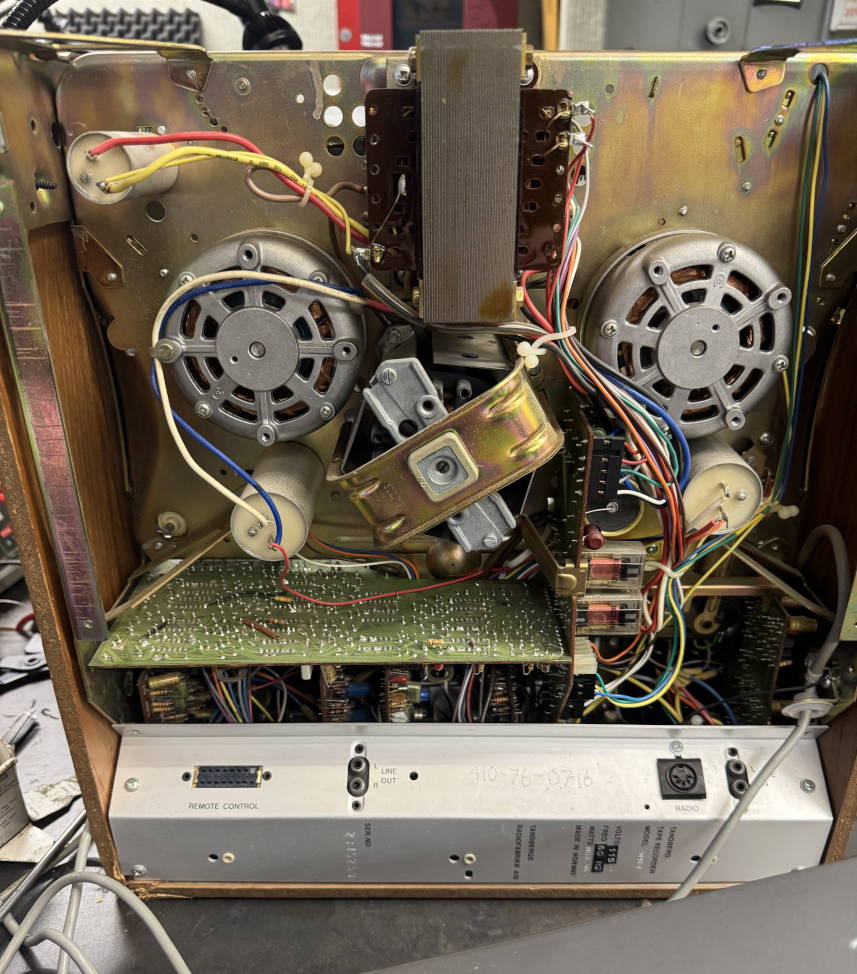
Look at how massively this thing is built! Two AC induction motors, a DC servo motor, and a HUGE power transformer.
David pulled off the solenoid's connector and cleaned years of oxidation from the contacts. Bingo! The solenoid pulled up the pinch roller with authority. We were back in business! While he had the covers off, he took a look around. The brake bands were clean and their solenoids worked perfectly, but he saw that the drive belt for the counter (right-hand side in the pic of the front) was on its last legs, loose and wobbly, so he replaced that as well. During the repairs, the tiny incandescent pilot lamp above the power switch failed, so I found a supplier online(!) and placed an order. It arrived the next day (Saturday!) so on Monday morning we were able to finish the repairs. Interestingly, every time he put the dress covers back on, the deck would stop working. After a couple of backs and forths, he found the source. David got it all working and buttoned up and I was ready to go back to work on the project.
MEANWHILE... THE LITTLE THINGS
Remember that I said that the supply reel clamp was missing on this deck? Over the years I’ve owned it, I’ve been poking around in various places, first at physical dealers and then online, looking for a replacement reel clamp for the supply side reel turntable. The fact that this fine machine was slightly hobbled by the loss of the clamp really nagged at me for some reason. Occasionally a complete turntable assembly or turntable assembly plus motor would show up, usually offered at an astronomical price. But the three parts I needed, the trident clamp, the tension spring, and threaded, closed retaining nut, were never available separately.
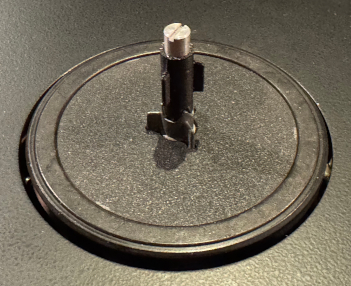
But right in time for this restoration, a fellow in Germany whose company goes by the name, “Decor Krueger,” offered these very parts on eBay. He uses 3D printing to reproduce the very trident clamp I needed and offers the spring and nut as well. To quote Captain Jack Aubrey from Master and Commander, the Far Side of the World, "That's the future. What a fascinating modern age we live in." I'll admit that I am totally amazed to find these parts. Who could have imagined that fifty years after this old school recorder was built, someone would remanufacture the exact parts I needed? We ordered a set of Mr. Kueger's replacement parts while the deck was in the shop for repairs and they arrived a week later. I did a little gentle fitting, relieving the center hole in the clamp slightly to allow it to fit over the turntable shaft, and then installed the assembly.
So here I sit in the studio control room, geeking out that for the first time in three decades the deck is complete. Behind me, the Tandberg is standing proudly upright again and a reel is playing back and being transferred safely and smoothly with the new parts in place. Thank you, David and thank you, Mr. Krueger! Somehow I find closing the circle on this old friend to be deeply satisfying.
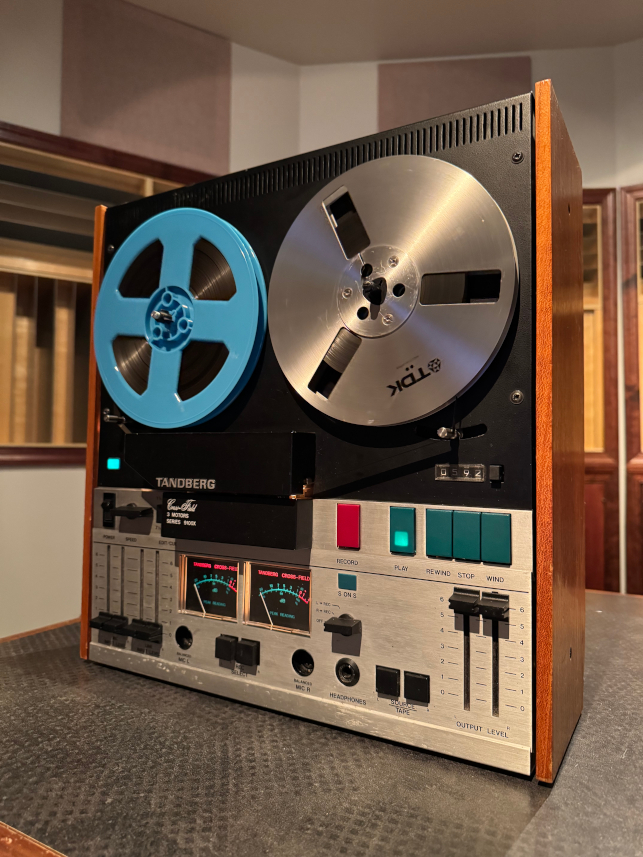
=
=